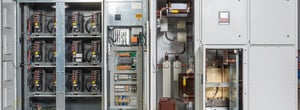
Variable Frequency Drives (VFD)
AuCom’s variable frequency drives (VFDs) provide precise motor control across a wide range of low and medium voltage applications. Built for reliability and performance, our drives support systems operating up to 13.8kV, delivering efficiency and flexibility to meet your operational needs.
VFDs enable you to adjust motor speed to match the exact demands of your process, making them ideal for industries such as mining, manufacturing, HVAC, and water and wastewater treatment. By optimising motor performance, VFDs also provide one of the most energy-efficient solutions for variable speed applications.
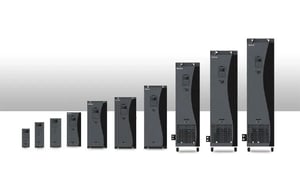
![]() |
4 - 450kW | ![]() |
380 - 460V |
Compact, efficient and powerful. H1 Series Drives support multiple motor types with advanced vector control, energy-saving features, and space-saving book-type design.
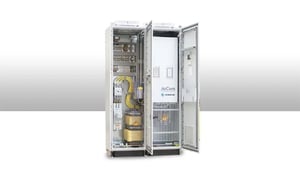
![]() |
55 - 4000kW | ![]() |
380 - 690V |
AuCom AFE Drives deliver low harmonic distortion and energy recovery in a compact, all-in-one design. Available in air or liquid cooling, the modular AFE platform ensures reliable, high-efficiency performance up to 4000 kW.
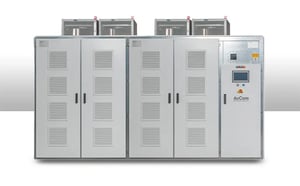
MVH2.0 Drive
![]() |
315 - 25,000kW | ![]() |
3.3 - 11kV |
The MVH2.0 delivers advanced performance, reliability, and intelligent control for demanding MV applications. With multilevel CHB technology, cloud-based monitoring, and scalable enclosures, it’s compact, connected, and built to perform.
Frequently Asked Questions
Here are answers to some of the most commonly asked questions about Variable Frequency Drives (VFDs), to help you better understand their functionality, applications, and benefits.
A Variable Frequency Drive (VFD) provides continuous speed control for electric motors by adjusting the frequency and voltage of the power supplied. This makes VFDs perfect for applications like pumps, fans, and conveyors where variable speeds and energy efficiency are crucial. In contrast, a Soft Starter only manages the startup of a motor by gradually increasing voltage to minimize inrush current and mechanical stress. Once the motor reaches full speed, a Soft Starter does not offer any speed control, making it suitable for applications that operate at a fixed speed.
Due to the phase-shifted multilevel cascade H-bridge technology, when operating the MVH2.0 with any motor, harmonic content does not need to be a concern.
The MVH2.0 remains within all limits specified by IEEE 519, and as the voltage level increases, the harmonic content decreases.
For example, an 11kV MVH2.0 system operates with 54 pulses in the SVPWM, delivering a smooth sine wave to the motor.
Yes, it is possible to have a different public grid supply voltage and motor-rated voltage. The MVH2.0 is equipped with a phase-shifted multilevel transformer in the input section, which transforms the input medium voltage to a low voltage ranging between 400V and 700V AC, depending on the motor's required output voltage.
By adding power cells in series, the MVH2.0 generates the necessary medium voltage for the motor in a floating grid configuration.
Thanks to the galvanic isolation provided by the transformer, the grid and motor operate independently, eliminating the need for the input and output voltages to match.
Important Note:
When the MVH2.0 is used as a Start Drive (MVH2.0S), the input and output voltages must be identical. After the motor reaches its nominal speed, the VFD synchronizes the floating grid with the public grid, requiring voltage consistency.
Hybrid cooling means, you can handle the heat dissipation of the transformer through a air cooling system and cool down the power electronic in the power cells by a water cooling system.
This can for example be interesting, if there is a need not to cool down that much heat by water, but the MVH2.0 needs to have power cells with a rated current of >800A. Power Cells with a current >800A need to be cooled by water, because of that much heat can not be cooled only by air. The transformer instead, can still get cooled by air.
A power cell bypass is an internal bypass mechanism within a single power cell. If a power cell experiences an internal fault, such as a faulty IGBT or a malfunction in the firing card, the bypass closes, allowing the faulty power cell to be shorted and enabling continued operation. In this situation, the VFD automatically shifts the neutral point, maintaining system operation at over 85% power.
A redundant power cell refers to the MVH2.0 being equipped with an additional power cell beyond the required number. If a power cell fault occurs, the faulty power cell is bypassed, and because of the redundant power cell, the VFD can continue to operate at 100% load.
To ensure this functionality, redundant power cells must also be equipped with the power cell bypass option.
When the required current exceeds 163A, the transformer windings and power cells become too large to fit within a single compact cabinet. Additionally, compact cabinets require double-sided access for maintenance, which may not be feasible in certain site conditions.
In such cases, the compact cabinet cannot be used, and a single-side access cabinet becomes necessary.