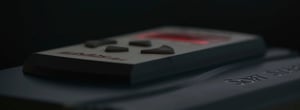
Soft Starters
AuCom offers a comprehensive range of low and medium voltage soft starters, designed to meet the needs of everything from basic motor starting to advanced motor control. Our solutions are built for operators of all experience levels, combining ease of use with reliable, consistent performance.
Compact and versatile, AuCom soft starters simplify installation and setup while providing smooth acceleration and deceleration control for three-phase motors. With models available to support current ratings from 200A to 1092A, we have solutions to suit a wide range of motor sizes and applications.
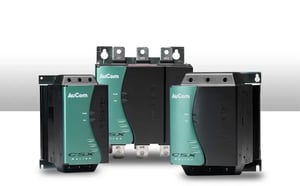
|
|
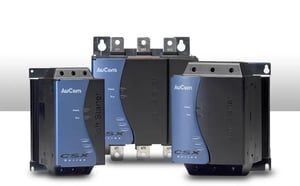
|
|
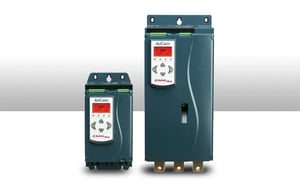
|
|
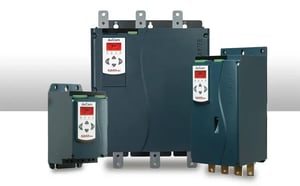
|
|
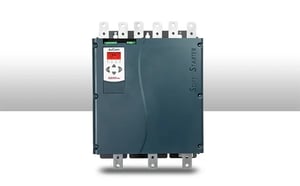
|
|
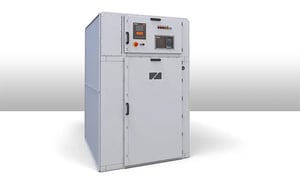
|
|
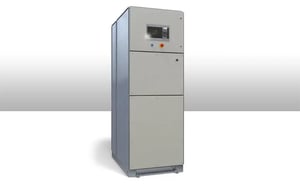
|
|
Frequently Asked Questions
Here are answers to some of the most commonly asked questions about Soft Starters, to help you better understand their functionality, applications, and benefits.
A soft starter is an electronic motor controller used on three phase squirrel cage induction motors. During motor starting, the soft starter controls the voltage or current supplied to the motor. Motor start performance is optimised by reducing the total start current while optimising the torque produced by the motor. Motor stopping can also be controlled by ramping down the output voltage over a predetermined time period. This is particularly useful for eliminating water hammer in pumping applications.
Soft starters use SCRs (silicon controlled rectifiers, also called thyristors), arranged back-to-back for each controlled phase of the soft starter. This provides phase angle control of the voltage waveform in both directions. Controlling the voltage controls the current supplied to the motor. The stepless control of motor terminal voltage eliminates the current and torque transients associated with electromechanical forms of reduced voltage starting, such as start-delta or autotransformer starters.
Soft start enhances motor start performance in many ways including:
- Smooth acceleration without the torque transients associated with electro-mechanical reduced voltage starters.
- Voltage or current is applied gradually, without the voltage and current transients associated with electro-mechanical reduced voltage starters.
- Lower start currents and/or shorter start times because constant current control gives higher torque as motor speed increases.
- Easy adjustment of start performance to suit the specific motor and load.
- Precise control over the current limit.
- Consistent performance even with frequent starts.
- Reliable performance even if load characteristics vary between starts (eg loaded or unloaded starts).
In addition to superior starting performance, soft starters also provide a range of features not available from other reduced voltage starters. This includes areas such as:
- Soft stop (which helps eliminate water hammer)
- Braking
- Motor and system protection
- Metering and monitoring
- Operating history and event logs
- Communication network integration
Soft starters need to be sized according to the required start duty for the connected motor. Factors include
- Start current (depends on machine type)
- Start duration (depends on machine type)
- Start frequency (depends on the process)
- Ambient temperature
AuCom offers two simple tools to assist in correct model selection
START HERE – Mobile App
Download the app and use the Quick Pick Starter Selection tool to get a recommended model based on typical application requirements.
WinSTART – PC modelling tool
Download the app to model tool to get a recommended model based on user specified starting conditions.
The AC53a Utilisation Code defines the current rating and standard operating conditions for a non-bypassed soft starter.
The soft starter’s current rating determines the maximum motor size it can be used with. The soft starter’s rating depends on the number of starts per hour, the length and current level of the start, and the percentage of the operating cycle that the soft starter will be running (passing current).
The soft starter’s current rating is only valid when used within the conditions specified in the AC53a code - the soft starter may have a higher or lower current rating in different operating conditions.
The AC53b Utilisation Code defines the current rating and standard operating conditions for a bypassed soft starter (internally bypassed, or installed with an external bypass contactor).
The soft starter’s current rating determines the maximum motor size it can be used with. The soft starter’s rating depends on the number of starts per hour, the length and current level of the start, and the amount of time the soft starter will be off (not passing current) between starts.
The soft starter’s current rating is only valid when used in the conditions specified in the AC53b code - the soft starter may have a higher or lower current rating in different operating conditions.
A Soft Starter is designed to smoothly start an electric motor by gradually ramping up the voltage, which reduces inrush current and mechanical stress. It is ideal for fixed-speed applications like compressors or large fans where minimizing wear during startup is key. Unlike a Variable Frequency Drive (VFD), which provides ongoing speed control and energy savings by varying motor speed throughout operation, a Soft Starter only functions during startup and cannot adjust the motor speed once full speed is reached.
Soft starters are 99.9% efficient while operating while drives have up to 3% losses.
AuCom soft starters can connect easily to Modbus, Profibus, DeviceNet or USB communication networks, using simple add-on communication interfaces
All communication interfaces allow you to:
- Control the soft starter
- Monitor the starter’s operational or trip status
- Monitor the starter’s current level and motor temperatures (using the motor thermal model)
Some protocols also allow you to read and write soft starter parameters (some soft starter models only). For installations with no existing network, AuCom offers WinMaster, a PC based software program while allows control., monitoring and parameter management via an RS485 or USB connection. Contact your local AuCom representative for more information.
Compared with star/delta starters, soft starters are much more flexible and provide a smooth start with no risk of transients.
- Star/delta starters offer limited performance because:
- Start torque cannot be adjusted to accommodate motor and load characteristics.
- There is an open transition between star and delta connection that results in damaging torque and current transients.
- They cannot accommodate varying load conditions (eg loaded or unloaded starts).
- They do not provide soft stop.
The main advantages of star/delta starters are:
- They may be cheaper than a soft starter.
- When used to start an extremely light load, they may limit the start current to a lower level than a soft starter. However, severe current and torque transients may still occur.
Compared with primary resistance starters, soft starters are more flexible and reliable.
- Primary resistance starters offer limited performance because:
- Start torque cannot be fine-tuned to match motor and load characteristics.
- Current and torque transients occur at each voltage step.
- They are large and expensive.
- Liquid resistance versions require frequent maintenance.
- Start performance changes as the resistance heats up, so multiple or restart situation are not well controlled.
- They cannot accommodate changing load conditions (eg loaded or unloaded starts).
- They cannot provide soft stop.
Compared with auto-transformer starters, soft starters are much more flexible and provide a much smoother start.
- Auto-transformer starters offer limited performance because:
- They offer only limited ability to adjust start torque to accommodate motor and load characteristics.
- There are still current and torque transients associated with steps between voltages.
- They are large and expensive.
- They are especially expensive if high start frequency is required.
- They cannot accommodate changing load conditions. eg, loaded or unloaded starts.
- They cannot provide soft stop.
Inside delta connection (also called six-wire connection) places the soft starter SCRs in series with each motor winding. This means that the soft starter carries only phase current, not line current. This allows the soft starter to control a motor of larger than normal full load current.
When using an inside delta connection, a main contactor or shunt trip MCCB must also be used to disconnect the motor and soft starter from the supply in the event of a trip.
Inside delta connection:
- Simplifies replacement of star/delta starters because the existing wiring can be used.
- May reduce installation cost. Soft starter cost will be reduced but there are additional cabling and main contactor costs. The cost equation must be considered on an individual basis.
Only motors that allow each end of all three motor windings to be connected separately can be controlled using the inside delta connection method.
Not all soft starters can be connected in inside delta.
Bypass contactors bridge out a soft starter’s SCRs when the motor is running at full speed. This eliminates heat dissipation from the SCRs during run state.
Some soft starters include built-in bypass contactors, others require an external bypass contactor.
Bypass contactors:
- Allow soft starters to be installed in sealed enclosures
- Eliminate the cost of forced-air cabinet ventilation
- Save energy by eliminating SCR losses during run
Bypass contactors bridge out a soft starter’s SCRs when the motor is running at full speed. This eliminates heat dissipation from the SCRs during run state.
Some soft starters include built-in bypass contactors, others require an external bypass contactor.
PFC capacitors can be sized using the following formula:
kVA (Cap) = √3 x Vline x 0.8 x motor no load current
Type 1 protection requires that, in the event of a short circuit on the output of a soft starter, the fault must be cleared without risk of injury to personnel. There is no requirement that the soft starter must remain operational after the fault.
Type 1 protection is provided by HRC fuses or a MCCB that form part of the motor branch circuit.
As a minimum, the protection method must be able to sustain the required motor start current.
Maximum fuse ratings for Type 1 motor protection are specified in UL and IEC standards.
Fuse | Rating (% Motor FLC) |
Fuse (non-time delayed) | 300% |
Fuse (time delayed) | 175% |
Type 2 protection requires that in the event of a short circuit on the output of a soft starter the fault must be cleared without risk of injury to personnel or damage to the soft starter.
Type 2 protection is achieved by using semiconductor fuses. These fuses must be able to carry motor start current and have a total clearing I2t < the I2t of the soft starter SCRs.
Semiconductor fuses for Type 2 circuit protection are additional to HRC fuses or MCCBs that form part of the motor branch circuit protection.
Refer to the soft starter’s Product Guide for semiconductor fuse recommendations.
The maximum distance between the starter and motor is determined by the voltage drop and the cable capacitance.
Voltage drop at the motor terminals must not exceed the limit specified in local electrical regulations when the motor is running fully loaded. Cabling should be sized accordingly.
Cable capacitance can be a factor for cable runs that are longer than 500 metres. Consult the soft starter manufacturer for advice - you will need to provide details about mains voltage, mains frequency and the soft starter model.
Yes, provided that the torque available from the motor under the new configuration is sufficient to accelerate the load. This may be difficult to determine and a trial may be required.
Soft starting is not suitable for applications where:
- the slip-ring motor was installed to deliver speed control.
- the load requires extreme start torque.
To develop starting torque, some resistance must remain in the rotor circuit during motor starting. This resistance must be bridged out using a contactor (AC2 rated for rotor current) once the motor is running close to full speed.
R (per phase) = 0.2 x (VR / √3 x IR )
Rotor resistance (R) can be sized using the following formula:
Where VR= open circuit rotor voltage
IR= full load rotor current
Power (per phase) = (20% x motor kW) / 3
Where VR= open circuit rotor voltage
IR = full load rotor current
Soft starters can be applied to the two most common types of two-speed motor. In both cases, separate motor protection must be provided for low and high speed operation.
Dahlander motors are special purpose motors often applied to two-speed compressor or fan applications. The motor windings are externally configured using contactors for high speed (dual star) and low speed (delta) operation.
Dual-winding motors have two separate pole configurations (eg 4 pole / 8 pole) on a common shaft. Each pole configuration (speed) is selected using an external AC3 rated contactor.
PAM (Pole Amplitude Modulated) motors alter the speed by effectively changing the stator frequency using external winding configuration. Soft starters are not suitable for use with this type of two-speed motor.
Yes, one soft starter can control two motors in sequence. However, the control and wiring is complex and expensive and any saving in soft starter cost is often outweighed by additional component and labour costs.
In order to use a soft starter in a sequential starting situation:
- Each motor must have a separate main contactor, bypass contactor and overload protection
- The soft starter must be suitably rated for the total start duty.
Yes. The circuit configuration and soft starter selection depends on the application.
Each motor must have its own overload protection.
If the motors are the same size and are mechanically coupled, a constant current soft starter can be used.
If the motors are different sizes and/or the loads are not mechanically interlocked, a soft starter with a timed voltage ramp (TVR) start profile should be used.
The combined motor FLCs must not exceed the soft starter FLC.
On their own, soft starters cannot run motors in reverse direction at full speed. However, forward and reverse operation can be achieved by using a forward and reverse contactor arrangement.
Some soft starters also provide a part speed function that runs the motor at slow speed in either forward or reverse, without a reversing contactor. However, reverse operation is limited to short periods at a fixed slow speed.
DC braking uses DC injection to slow the motor.
When the soft starter receives a stop command, it slows the motor to approximately 70% of full speed. The starter then applies maximum brake torque to stop the motor in the programmed time.
Compared with soft braking, DC braking:
- Does not require the use of a DC brake contactor
- Controls all three phases so that the braking currents and associated heating is evenly distributed through the motor.
Need help? Contact us
Soft braking is one of two techniques used by soft starters to shorten motor stopping time. The other technique is DC braking.
Soft braking uses reversing contactors on the input of the soft starter. When the soft starter receives a stop command, it operates the reversing contactors and the motor is effectively soft started in the reverse direction. This applies a braking torque to the load.
Compared to DC braking, soft braking:
- Causes less motor heating
- Provides more braking torque for a given current
Soft braking is better for extremely high inertia loads.
Need help? Contact usSoft starters can limit start current to any desired level. However, the minimum level of start current for a successful start depends on the motor and load.
To start successfully, the motor must produce more acceleration torque than the load requires, throughout the start.
Reducing the start current also reduces the torque produced by the motor. The start current can only be lowered to the point where the torque output remains just greater than the load torque requirement.
The likely start current can be estimated from experience, but more precise predictions require analysis of motor and load speed/torque curves.
Successful start:
Unsuccessful start:
Need help? Contact us
Yes, soft starters can start motors that are already rotating.
In general, the faster the motor is rotating in the forward direction, the shorter the start time will be.
If the motor is rotating in the reverse direction, it will be slowed to a standstill and then accelerate forwards. Allow for the extended start time when rating the soft starter.
No special wiring or soft starter setup is required.
Need help? Contact us
No. There are different styles of soft starter which control the motor in different ways and offer different features.
1. Single Phase Control
These devices reduce torque shock at start but do not reduce start current. Also known as torque controllers, these devices must be used in conjunction with a direct on-line starter.
2. Two Phase Control
These devices eliminate torque transients and reduce motor start current. The uncontrolled phase has slightly higher current than the two controlled phases during motor starting. They are suitable for all but severe loads.
3. Three Phase Control
These devices control all three phases, providing the optimum in soft start control. Three phase control should be used for severe starting situations.